Als alles voorbereid is, is het daadwerkelijk op elkaar lijmen van de vleugelschalen niet zoveel werk meer. Dit kan dan ook na afloop van het normale werk gedaan worden en we beginnen om 4 uur ‘s middags.
Voor daadwerkelijk verlijmd wordt, wordt nog een hoogtemeting van de beide schalen gedaan, om te zien of het overal gaat passen. Deze metingen worden om de halve meter herhaald en worden op drie meest kritische plekken gedaan, neuslijst, achterlijst en ligger.
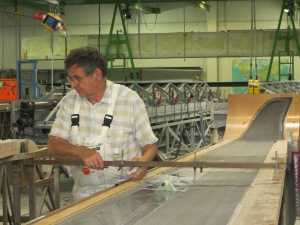
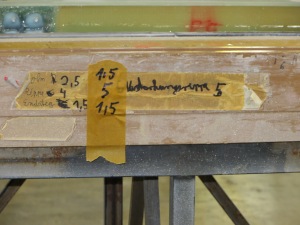
Het verlijmproces is steeds weer hetzelfde; de plaatsen die moeten worden verlijmd zijn al geschuurd en worden nu voorgestreken met dunne hars en daarna wordt er een “dijkje” ingedikte hars op gesmeerd.
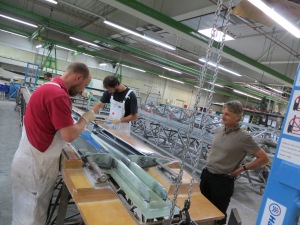
Het enige verschil met andere delen is dat de hars nu in 5 liter emmers wordt gemixed, in plaats van halve liter bekers. De aangedikte hars wordt in knijpzakken gedaan, gemaakt van opengesneden vuilniszakken.
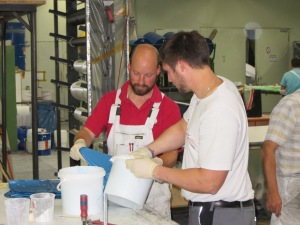
Het aanbrengen van een geschatte 100 strekkende meter aan hars…
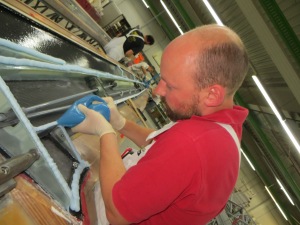
Hierna wordt de hars glad afgestreken en wordt er nog een dunne laag op de onderkant aangebracht.
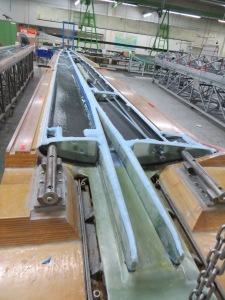
Dan wordt de bovenschaal aan de hijskraan gehangen en omhoog getakeld. Daarna wordt de bovenschaal gedraaid en wordt de onderschaal eronder geschoven, waarna de bovenschaal langzaam omlaag getakeld wordt. Er worden bij het takelen nog twee hefwagens gebruikt als backup, omdat de mallen ca. 1,5 ton wegen. Daardoor hebben we 6 man nodig om de vleugelmallen te draaien, twee aan de kranen, twee aan de hefwagens en twee om te draaien en te begeleiden bij het laten zakken van de mal.
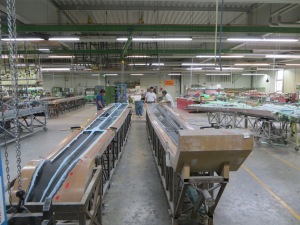
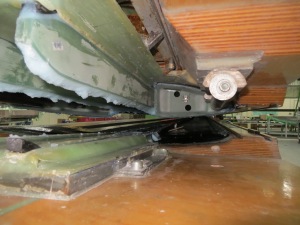
Na het sluiten worden op de mal nog zo’n 50 lijmklemmen aangebracht, die samen met het gewicht van de bovenschaal de gewenste druk brengen. Aan de liggerstompen en rondom de wortelribben kan nu alvast de overtollige hars worden weggestreken, dat scheelt later erg veel werk. De mal sluit netjes en nu wordt het proces herhaald voor de rechter kant. Om ca. 2100 uur zijn we klaar met de tweede vleugel en daarna is het tijd voor een vreugdebiertje.